A Guide Report for Briquette Manufacturing Process
As the development of our society, the world population is increasing day by day which results the increasing of the energy demand. People has realized the lack of natural energy sources can not meet the demand, developing renewable energy becomes urgent.Briquette Fuel VS Traditional Fuel
Briquette fuel
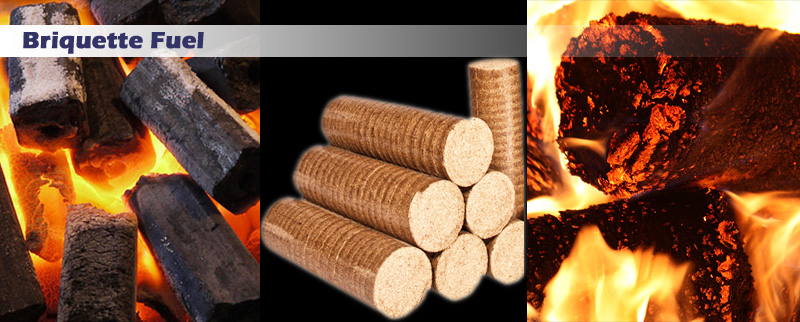
Briquette is usually in the shape of solid cylinder or hollow hexagon, the diameter ranges from 12mm to 70mm, and the length is usually in 50-80mm. Commonly, briquette fuel is formed through a series briquette manufacturing process. Both of biomass and biomass-free materials can be used for making briquette, and the different type raw materials decides the different type briquettes.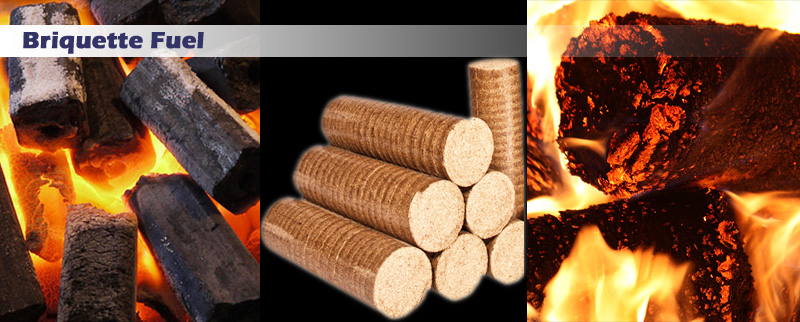
- Biomass briquette ——Biomass briquette fuel means that making the biomass raw materials into fuel, the general biomass raw materials includes agro and forestry residues like straws, sawdust, rice husk, bagasse, sorghum shell, peanut shell, wood shavings, bamboo dust, coconut shell, twigs, barks, corn robs etc; daily wastes like newspapers, waste cardboard, waste papers, paper pulp etc; barn wastes like horse manure, cattle manure and goat manure.
- Charcoal briquette ——Charcoal briquette is the residue dark or brown solid porous fuel after incomplete combustion of wood or wood materials or after pyrolysis in isolation from air. Charcoal is divided into three different types according to the raw material difference, respectively are hard carbon made from beech, oak etc, soft carbon made from elm, linden and willow etc, machinery charcoal made from sawdust briquette etc. But due to national policy for environmental protection, the first two kinds of charcoal has not been processed any more.
Traditional fuel
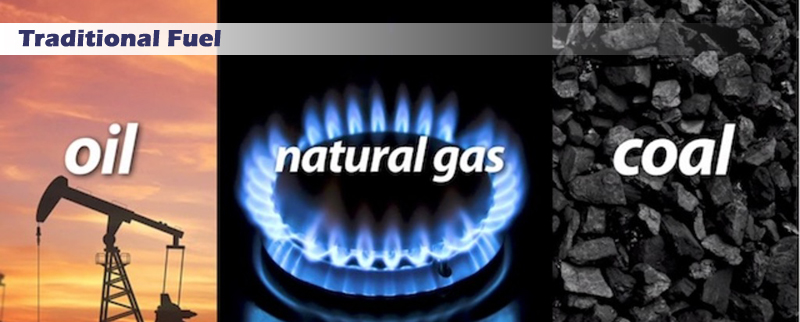
Traditional fuel is also called conventional energy, meaning the disposable non-renewable conventional energy which has been massively developed and widely used like coal, oil, natural gas etc. Coal is a flammable black or brown organic sedimentary rock which formed after thousands of years; oil, or petroleum, is one kind of viscous dark brown liquid, is called as the blood of industry, usually used as engine fuel.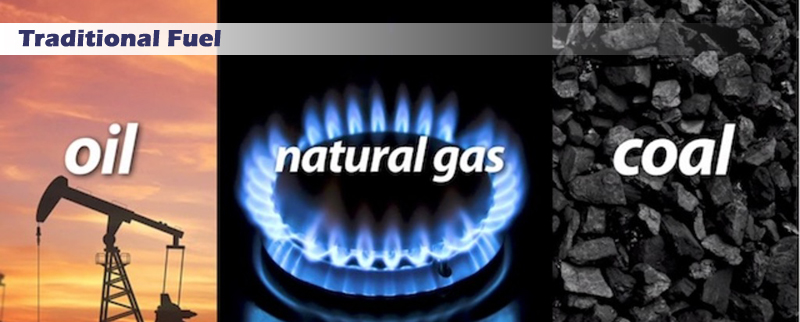
Generally, people process the coal into briquette for convenient use, so the coal and lignite are usually used for making coal briquette or lignite briquette, which is also called non-biomass briquette or coal briquettes, widely used in large power generation station.
As we all know that fossil fuel is not inexhaustible, and it needs a very long time for formation and large cost for exploiting. Most importantly, the fossil fuel whether it is through the briquette manufacturing or not produce bad smoke into the air in the combustion, which is bad for our health and environment. While the biomass briquette, through complete briquette manufacturing process, has a high density, uniform size, burning fully without bad smoke produced, is the best substitute of the traditional fuel.
Briquette Making Principle
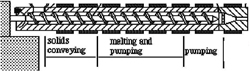
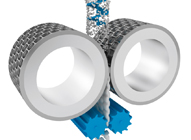
Differ from the biomass briquette manufacturing, coal briquette is made under the principle of carbonization which is also called dry distillation, and non-biomass briquette depends on the coal briquette press by mixing the water and coal fines according to the certain proportion.
Briquette Manufacturing Process Art
The lack of one-size-fits-all process means that the briquette manufacturing process is more an art rather than science.
Biomass Briquette Manufacturing Process
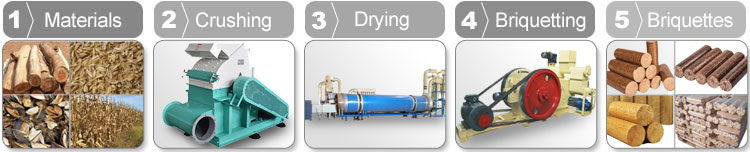
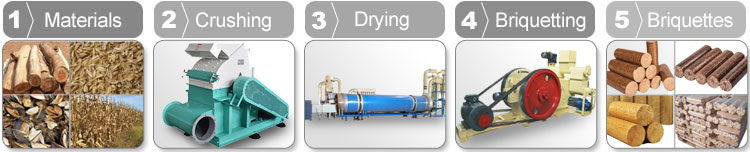
- Raw material: One key question for biomass briquette manufacturing process is the supplying and storing of the raw material. You have to make sure the raw material supplying can provide you the materials fro longer time. Some raw materials will be influenced by the season and the climate, storing raw materials well is very important as well, trying to keep the raw material dry will be very helpful for your later briquette production.
- Crushing and drying: Raw material crushing and drying are the essential in the biomass briquette manufacturing process due to make the size and moisture content meeting the requirements of briquetting processing. If the raw material is in powder, the crushing processing can be not equipped. For drying, natural drying and machinery drying can be optional according to your briquette applications. Natural drying is enough for self-use, and machinery drying is better for commercial use.
- Briquetting: As the most key step of biomass briquette manufacturing process, choosing a suitable briquette press or not decides the final quality of the briquette.
- Cooling and packing: The fresh finished briquette should be cooled after briquetting before packing them into bags or box due to the high temperature. After cooling, the quality guarantee period of briquette can be prolonged with 40%.
Based on the difference standards, the briquetting machinery can be divided into different types. According to the working principle, it has two kinds, including punching briquette press and screw briquette press, the former is based on the machinery stamping shock on the raw materials and forms them into density briquette; while the latter adopts the screw rob to pushing the raw materials into the forming sleeve to briquetting.
Both of these two briquette press can be used singly, usually they are used in briquette production line for making better briquette quality. Our designed briquette production line has small, medium and large scale, and due to the different raw material characters, the biomass briquette manufacturing process is no the same exactly, thus we can customize the briquette production line according to the requirements and actual situation of the clients from different regions.
Charcoal Briquette Manufacturing Process
- For the raw materials of charcoal briquette manufacturing process, you can use the finished biomass briquettes directly. Also you can use the organic wastes, and remember to dry them firstly.
- Put the collected biomass briquette or prepared organic wastes into the kiln, and control the combustion temperature and time.
- After the combustion which is pre-set, the charcoal briquette is finished. Then cool them for later use.
Option 2
- Collecting the charcoal fines and adjusting the moisture of charcoal fines by adding water.
- Using the briquette machine to compress the charcoal briquette.
-
Cooling the finished charcoal briquette before packing them into bags for later use.
Coal Briquette Manufacturing process
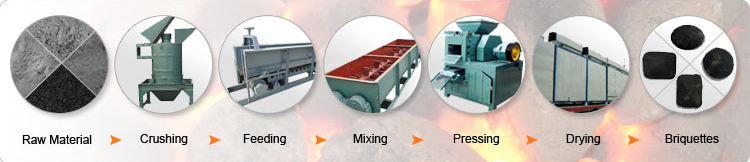
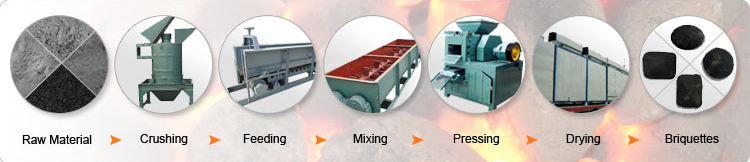
- Crushing the coal or lignite into fines.
- Adjusting the moisture of coal fines or lignite fines.
- Press the fines with the coal rods machine.
- Drying the finished coal briquette naturally.